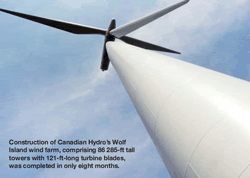
WALKERTON, ONT.-BASED concrete contractor MAHCRETE has been building wind tower foundations since 2005, hut its largest project to date Canadian Hvdro’s \Xolf Island Wind Farm in Kingston, Ont. The ‘Xolf Island facility consists of 86 wind towers, each 285 ft from base to huh and each supporting 12 1-ft-long blades. MATTCRETE built the foundations for all 86 towers in only seven months (from September 2008 to March 2009), therefore efficiency and coordinated efforts were critical to the $480-million project’s success.
Each foundation used about 664 cuyds of concrete with a design compressive strength of just over 5000 psi. The mix design included a high slag content that helped control the heat generated by cement hydration and reduce cracking of the massive concrete slabs. But early strength development was important to keep the project on schedule. MA! ICRETE president 1att Jagelewski says, We needed to reach 4061 psi by 21 days to enable folks to set the towers on time.”
The typical foundation is octagonal, about 56 ft across, 6 ft 8 in. thick, and resting on bedrock. Two of the towers were located in areas with sandy soil; their foundations were each
supported by 24 caissons drilled to bedrock. A l7-ft-diarneter concrete cylinder extends about 6 ft above from the center of the octagon, containing anchor bolts to which the tower structure is attached. MATTCRETE designed and fabricated its own steel forms for the foundations, using one
piece of formwork for each side of the octagon. The forms were lifted into place using a crane, then bolted together to create the desired angles and tied back with telescoping adjustable braces.
Once the formwork was in place, MATTCRETE supervised a subcontractor’s installation of steel reinforcement before placing the concrete using two boom pumps.
Each foundation used about 664 cuyds of concrete with a design compressive strength of just over 5000 psi. The mix design included a high slag content that helped control the heat generated by cement hydration and reduce cracking of the massive concrete slabs. But early strength development was important to keep the project on schedule. MA! ICRETE president 1att Jagelewski says, We needed to reach 4061 psi by 21 days to enable folks to set the towers on time.”
The typical foundation is octagonal, about 56 ft across, 6 ft 8 in. thick, and resting on bedrock. Two of the towers were located in areas with sandy soil; their foundations were each
supported by 24 caissons drilled to bedrock. A l7-ft-diarneter concrete cylinder extends about 6 ft above from the center of the octagon, containing anchor bolts to which the tower structure is attached. MATTCRETE designed and fabricated its own steel forms for the foundations, using one
piece of formwork for each side of the octagon. The forms were lifted into place using a crane, then bolted together to create the desired angles and tied back with telescoping adjustable braces.
Once the formwork was in place, MATTCRETE supervised a subcontractor’s installation of steel reinforcement before placing the concrete using two boom pumps.
Properly consolidating the concrete was an important step, ensuring that the foundations were strong and stable enough to support the towers. “You can’t vibrate it too much or the stone sinks,” Jagelewski says, “hut you have to get it around all the rebar and anchor bolts
without leaving voids.”
NIATTCRETE used a variety of vibrating equipment manufactured by Oztec Industries, Port Washington, N.Y., to keep the project moving. Three were Oztec Model GV-SW wheelbarrow units with 5-hp Honda gasoline engines, and another four were Model BP-5O, the vibrator manufacturer’s largest backpack vibrators, with 2 ½ -hp Honda engines. Both of these Oztec per units feature the company’s “speed-up” transmission, which maintains a vibration rate of 10,000 to 12,000 vpm, and both will run for an hour or more on a full tank of gas. With each of these vibrators, crews used 16-ft flexible shafts with 2½ -in.-diameter steel heads. MATTCRETE also kept about a dozen 214 -lip electric vibrators on hand for backup.
without leaving voids.”
NIATTCRETE used a variety of vibrating equipment manufactured by Oztec Industries, Port Washington, N.Y., to keep the project moving. Three were Oztec Model GV-SW wheelbarrow units with 5-hp Honda gasoline engines, and another four were Model BP-5O, the vibrator manufacturer’s largest backpack vibrators, with 2 ½ -hp Honda engines. Both of these Oztec per units feature the company’s “speed-up” transmission, which maintains a vibration rate of 10,000 to 12,000 vpm, and both will run for an hour or more on a full tank of gas. With each of these vibrators, crews used 16-ft flexible shafts with 2½ -in.-diameter steel heads. MATTCRETE also kept about a dozen 214 -lip electric vibrators on hand for backup.
Jagelewski says everyone involved with the project was pleased with the efficiency of construction. “There’s a long lead time needed to get the wind towers and turbines—they have to he ordered about a year in advance—so Canadian Hydro was anxious to get them installed as soon as they were available. But everybody was amazed that we could place more than
73,000 cu yds of concrete in less than eight months.”
73,000 cu yds of concrete in less than eight months.”
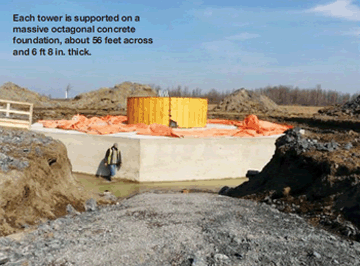
No comments:
Post a Comment